Opcenter APS – Advanced Planning and Scheduling Software
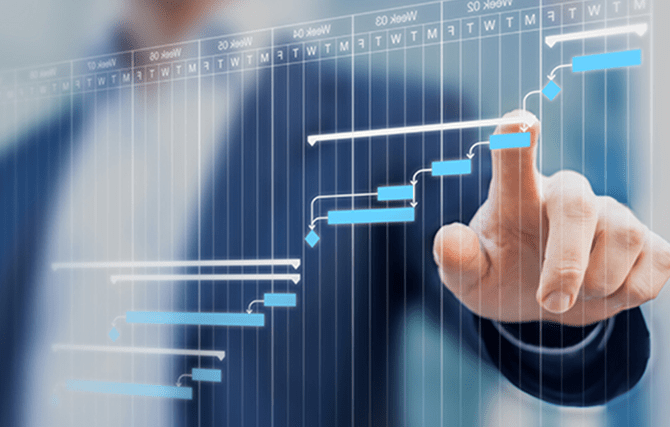
INTRODUCTION

Opcenter APS is a powerful capacity planning and scheduling tool that enables process manufacturers to
- Meet shorter lead times
- Maximize the usage of labor and equipment resources along the production lines
- Respond to real-time events, such as inventory shortages and equipment failures
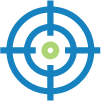
Be Accurate
Schedule activities down to the granular level based upon real-time actionable data
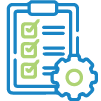
Get Specific
Employ complex algorithms and unique sequencing rules for each batch job
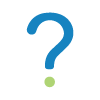
Consider Choices
Adjust schedules based upon ‘What If Scenarios’
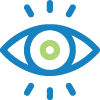
Be Visual
Take advantage of Gantt chart visualization features
SAMPLE OF SCHEDULING FUNCTIONS

Opcenter APS is a finite capacity scheduling tool based on a detailed model of the plant, which creates schedules in minutes.
- Optimize schedules based upon business rules (date priority, setup optimization, group by attributes, reduce bottlenecks).
- Consider restrictions (e.g. machine, labor, tooling, setup times).
- React to real time downtime, shift changes, material shortages, and changes to sales order delivery dates.
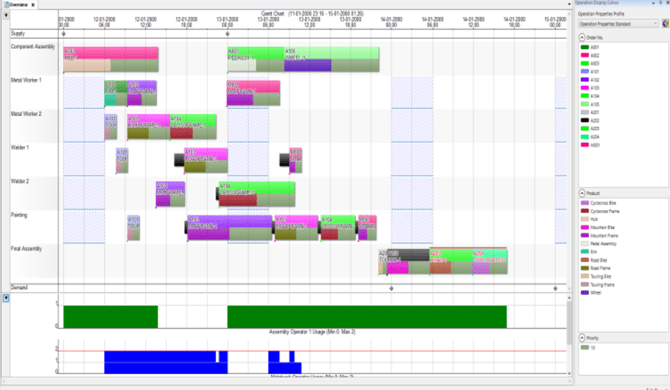
Opcenter APS considers key supply and demand factors in your manufacturing process when planning and scheduling batch jobs across multiple facilities:
- Machines: Consider capacity and availability per machine, schedule and plan based on your actual productive force.
- Labor: Consider what activities, time and resources are needed to fulfill each production order.
- Capacity: Consider the work capacity on your production floor (number of available workers and skill level).
- Demand requirements (customer needs): Consult historical data on the demand of each client, plan and schedule based on the needs of your clients.
OPCENTER APS BENEFITS

Opcenter APS give users the ability to perform ‘What If Scenarios’ using planned batch jobs created by the Master Production Scheduling module (MPS). Based upon the planned batch jobs and inventory levels, the application supports one’s lean initiative by
- Better utilizing equipment and labor resources.
- Providing faster what-if scenario modeling.
- Reducing equipment setup and changeovers.
- Reducing inventory levels and work-in-progress.
- Offering full visibility to batch job constraints and progress.
CONTACT US / REQUEST A DEMO

Let’s see if BatchMaster Software has the right software solution for your needs. Contact Us to share something about your operations and software needs with our consultants or Request A Demo of one of our software applications.