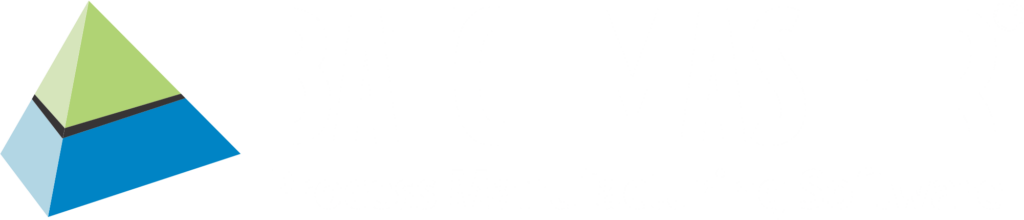
Food Process Manufacturing ERP Software
- Inventory management
- Traceability
- Quality control
- Production management
- Formulation
- Industry specific compliance
- Planning & Scheduling
Food Manufacturing Solutions for Your Food Vertical


Bakeries & Snack

Beverages

Dairy

Dressings & Sauces

Spices &
Seasonings

Flavors &
Additives

Frozen &
Packed Foods

Confectionery &
Chocolate
Key Modules Found in Our Food ERP Software Applications

Process
Manufacturing
Modules
BatchMaster
ERP Solution
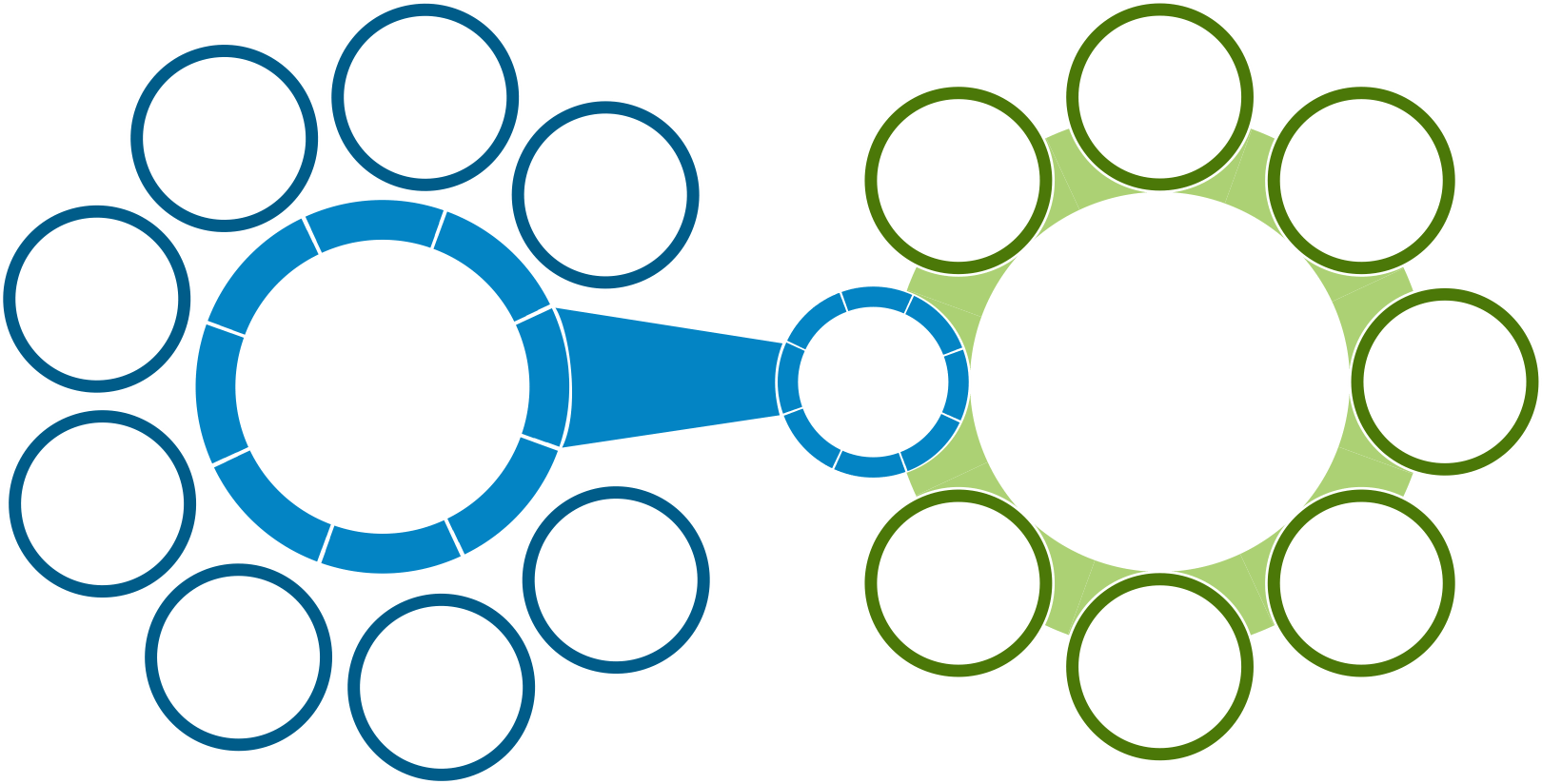
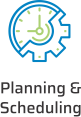

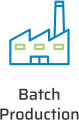


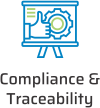
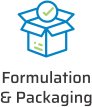
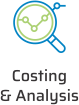
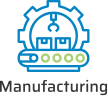
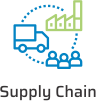


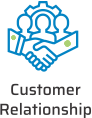


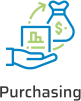
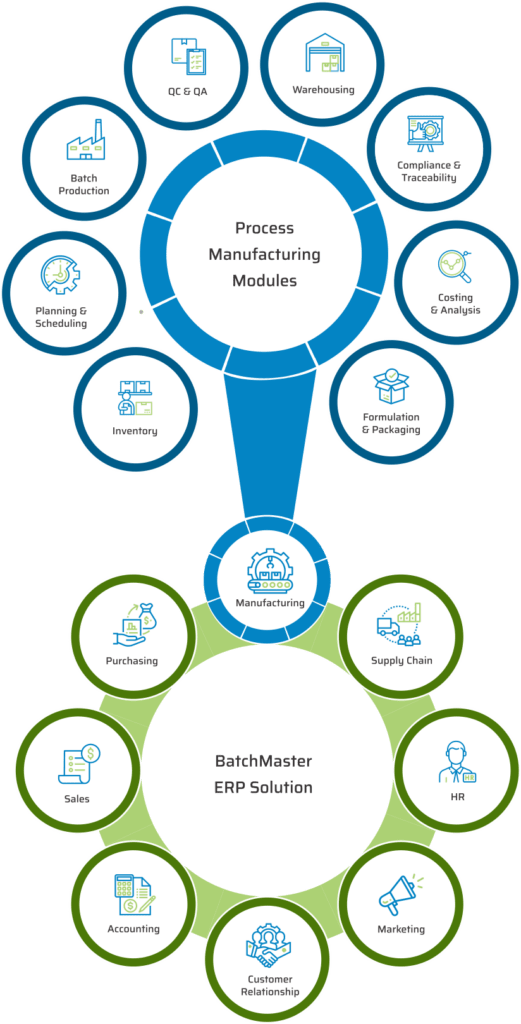
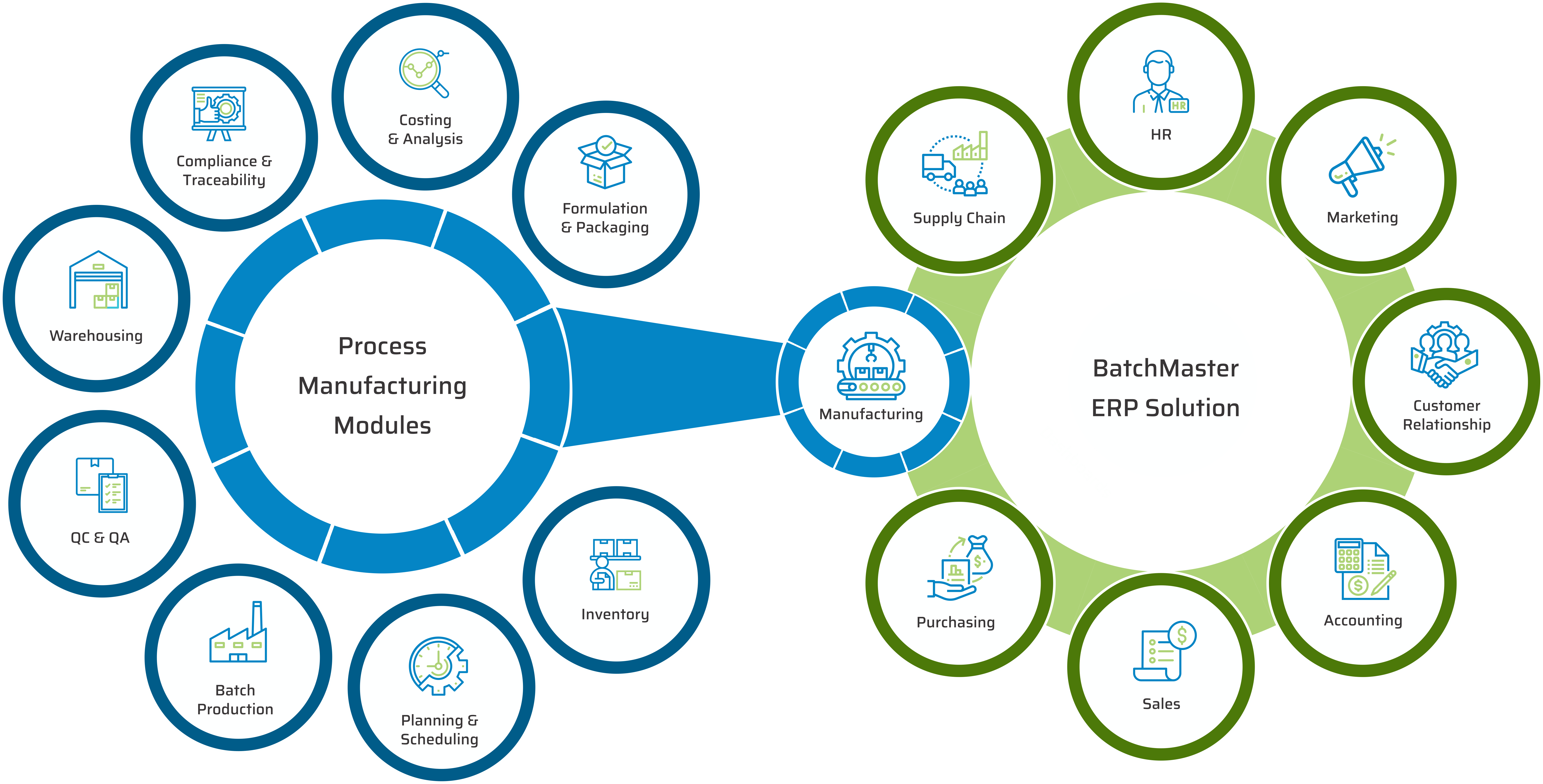
Food Processing Software That Will Change the Way You Work

- Inventory
- Traceability
- Quality
- Production
- Formulation
- Compliance
- Planning & Scheduling
Inventory
Key features include:
- Attribute Management: Maintain records for allergens, safety, certifications, and industry-specific documents.
- Smart Allocation: Allocate inventory based on expiry dates and quality status.
- Batch Adjustments: Dynamically adjust batch jobs according to inventory characteristics.
- Mobile Warehousing: Execute warehousing tasks efficiently using mobile devices.
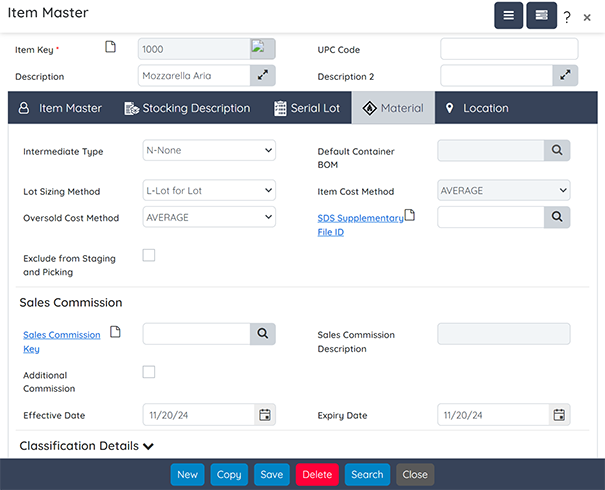
Traceability
Key features include:
- Automatic Lot Numbering: Assign lot numbers automatically during receiving and production.
- Lifecycle Tracking: Capture and validate lot numbers at every stage of production.
- Quick Searches: Perform bi-directional searches using an intuitive graphical tool.
- Recall Management: Generate barcoded labels (e.g., product labels, pallet licenses) to further streamline operations.
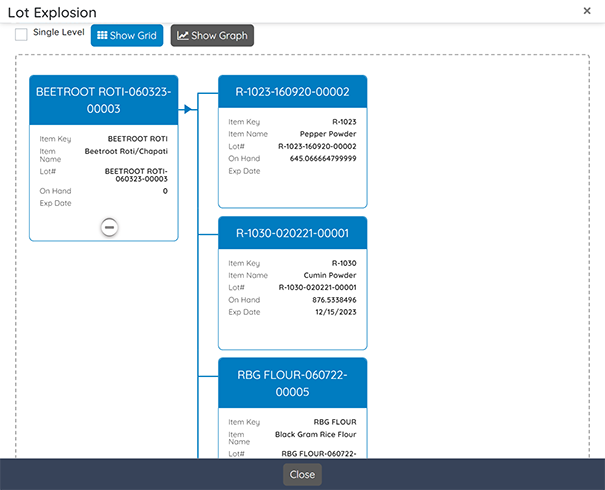
Quality
Integrate quality control and assurance throughout all processes, ensuring product safety and compliance.
Key features include:
- QC Testing: Set up quality control tests with specified tolerance and sample values.
- Inspection Plans: Execute comprehensive inspection plans and checklists.
- Documentation: Generate Certificates of Analysis (COA) and manage production deviations.
- Issue Management: Address customer complaints and nonconformance situations effectively.
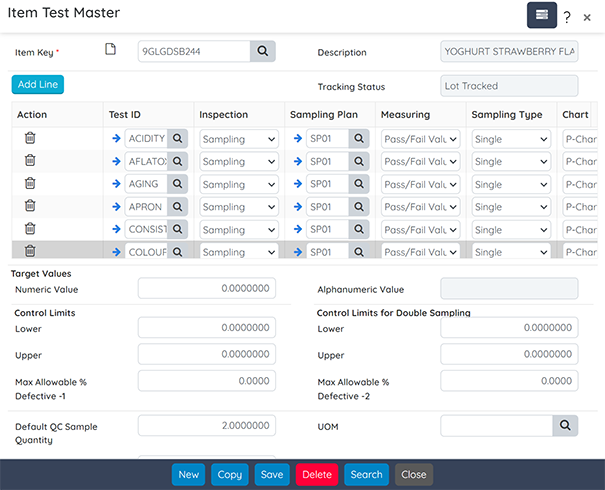
Production
Optimize production processes for intermediates and finished goods, including co-products and by-products.
Key capabilities include:
- Dynamic Job Scheduling: Link and schedule dependent batch jobs based on resource availability.
- Resource Management: Manage equipment capacities and resource allocations efficiently.
- Deviation Capture: Record and address deviations during production runs.
- Inventory Backflushing: Automatically backflush inventory for completed jobs.
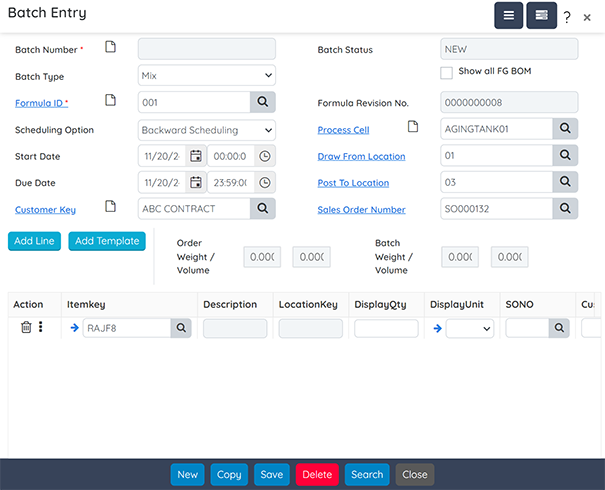
Formulation
Facilitate the management of product specifications across multiple versions and formulations.
Key features include:
- Dynamic Adjustments: Modify ingredient weights and volumes to achieve target properties.
- Cost Analysis: Account for fixed and variable labor and consumable costs.
- Specification Comparison: Analyze and compare different product specifications.
- Workflow Approval: Employ multi-level workflows for formulation approvals.
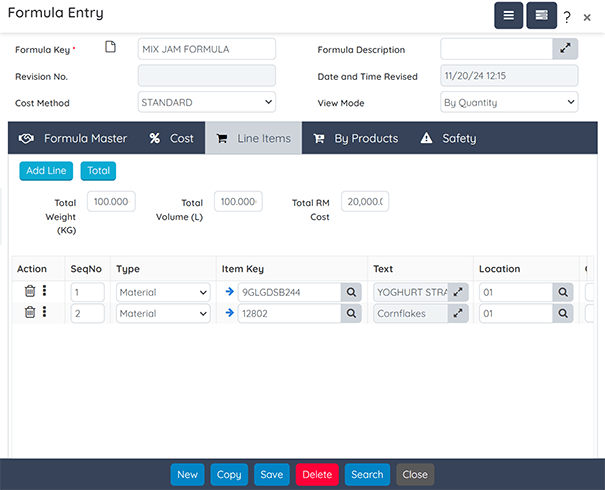
Compliance
Ensure adherence to federal and industry-specific regulations throughout every process.
Key functionalities include:
- Real-Time Alerts: Notify formulators when specifications exceed established levels.
- Data Capture: Mandate the collection of item, user, and location data for compliance (CFR 11).
- Audit Trail Maintenance: Maintain transactional history for auditor reporting, including Master Batch Records.
- Label Generation: Automatically generate required product and safety labels and documents.
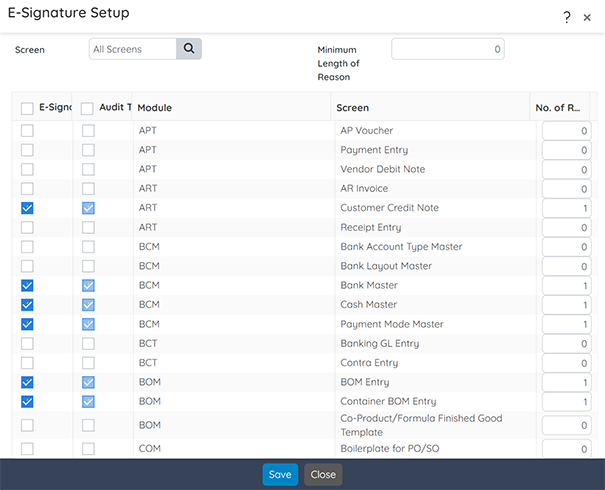
Planning & Scheduling
Optimize production and procurement processes to meet demand effectively.
Key capabilities include:
- Comprehensive Planning: Establish short, medium, and long-range planning periods.
- Facility Management: Plan production by facility or across multiple locations.
- Supply and Demand Consolidation: Streamline supply and demand management across facilities.
- What-If Analysis: Perform scenario analysis while planning production schedules.
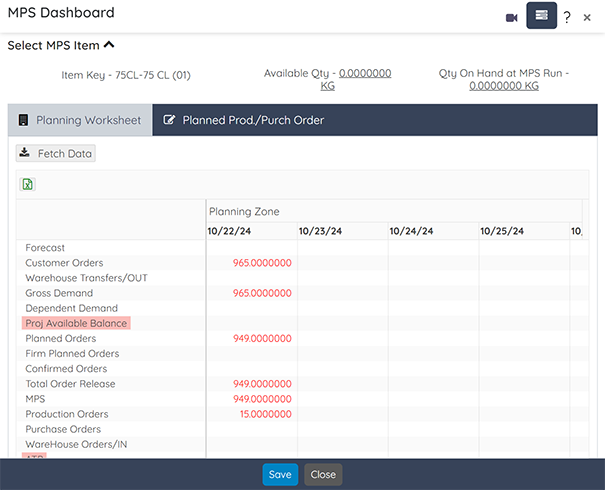
Inventory
Key features include:
- Automatic Lot Numbering: Assign lot numbers automatically during receiving and production.
- Lifecycle Tracking: Capture and validate lot numbers at every stage of production.
- Quick Searches: Perform bi-directional searches using an intuitive graphical tool.
- Recall Management: Generate barcoded labels (e.g., product labels, pallet licenses) to further streamline operations.
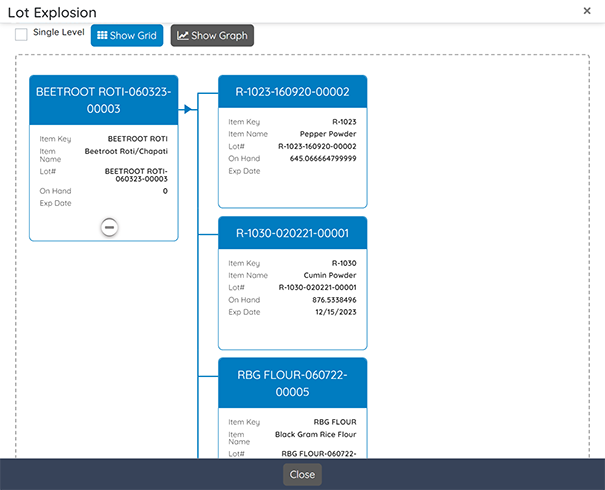
Quality
Key features include:
- QC Testing: Set up quality control tests with specified tolerance and sample values.
- Inspection Plans: Execute comprehensive inspection plans and checklists.
- Documentation: Generate Certificates of Analysis (COA) and manage production deviations.
- Issue Management: Address customer complaints and nonconformance situations effectively.
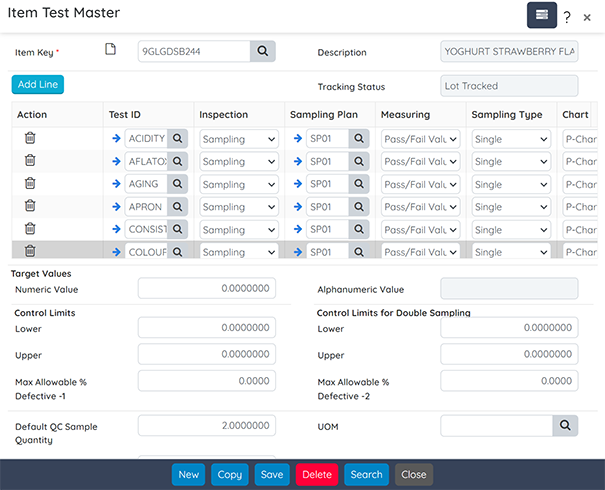
Production
Key capabilities include:
- Dynamic Job Scheduling: Link and schedule dependent batch jobs based on resource availability.
- Resource Management: Manage equipment capacities and resource allocations efficiently.
- Deviation Capture: Record and address deviations during production runs.
- Inventory Backflushing: Automatically backflush inventory for completed jobs.
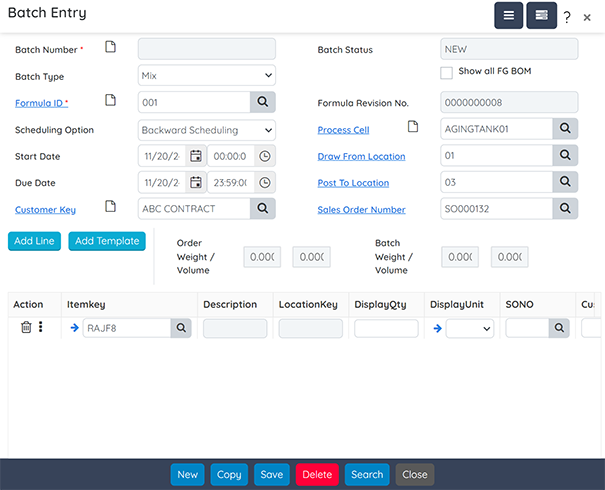
Formulation
Key features include:
- Dynamic Adjustments: Modify ingredient weights and volumes to achieve target properties.
- Cost Analysis: Account for fixed and variable labor and consumable costs.
- Specification Comparison: Analyze and compare different product specifications.
- Workflow Approval: Employ multi-level workflows for formulation approvals.
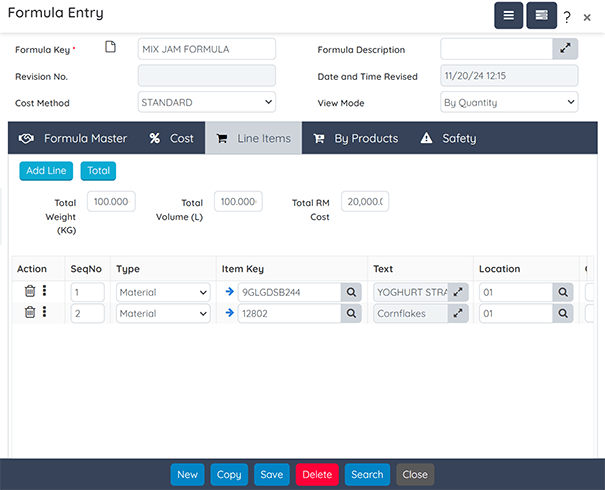
Compliance
Key functionalities include:
- Real-Time Alerts: Notify formulators when specifications exceed established levels.
- Data Capture: Mandate the collection of item, user, and location data for compliance (CFR 11).
- Audit Trail Maintenance: Maintain transactional history for auditor reporting, including Master Batch Records.
- Label Generation: Automatically generate required product and safety labels and documents.
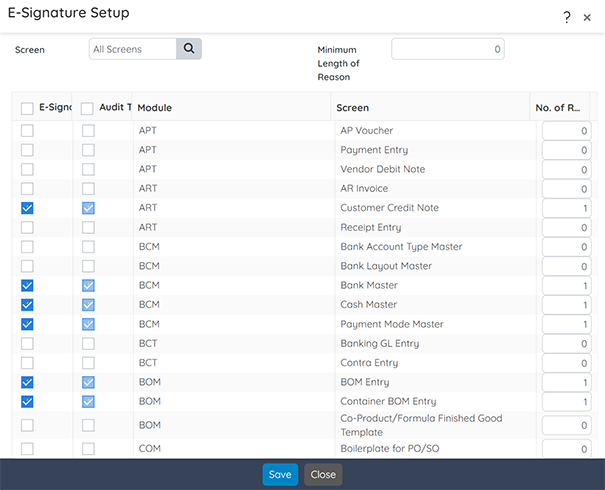
Planning & Scheduling
Optimize production and procurement processes to meet demand effectively.
Key capabilities include:
- Comprehensive Planning: Establish short, medium, and long-range planning periods.
- Facility Management: Plan production by facility or across multiple locations.
- Supply and Demand Consolidation: Streamline supply and demand management across facilities.
- What-If Analysis: Perform scenario analysis while planning production schedules.
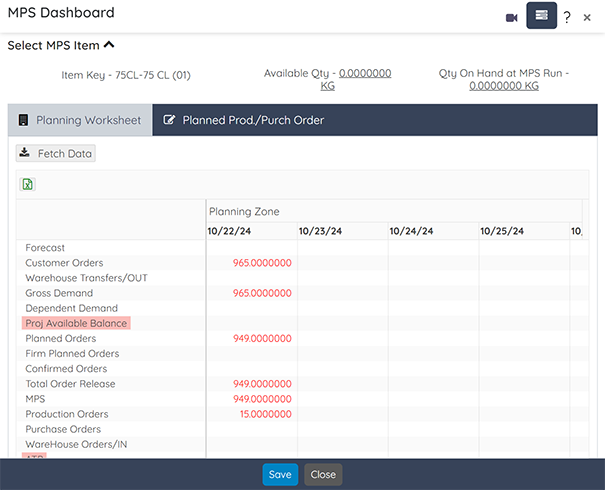
RUN BATCHMASTER MANUFACTURING WITH THESE LEADING FINANCIALS

DO NOT be forced into replacing your current financials to run a new ERP solution! Add industry specific manufacturing capabilities to these leading financial applications.
BatchMaster
Manufacturing
Application
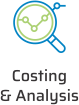
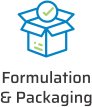
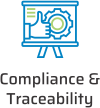


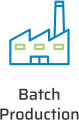
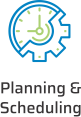

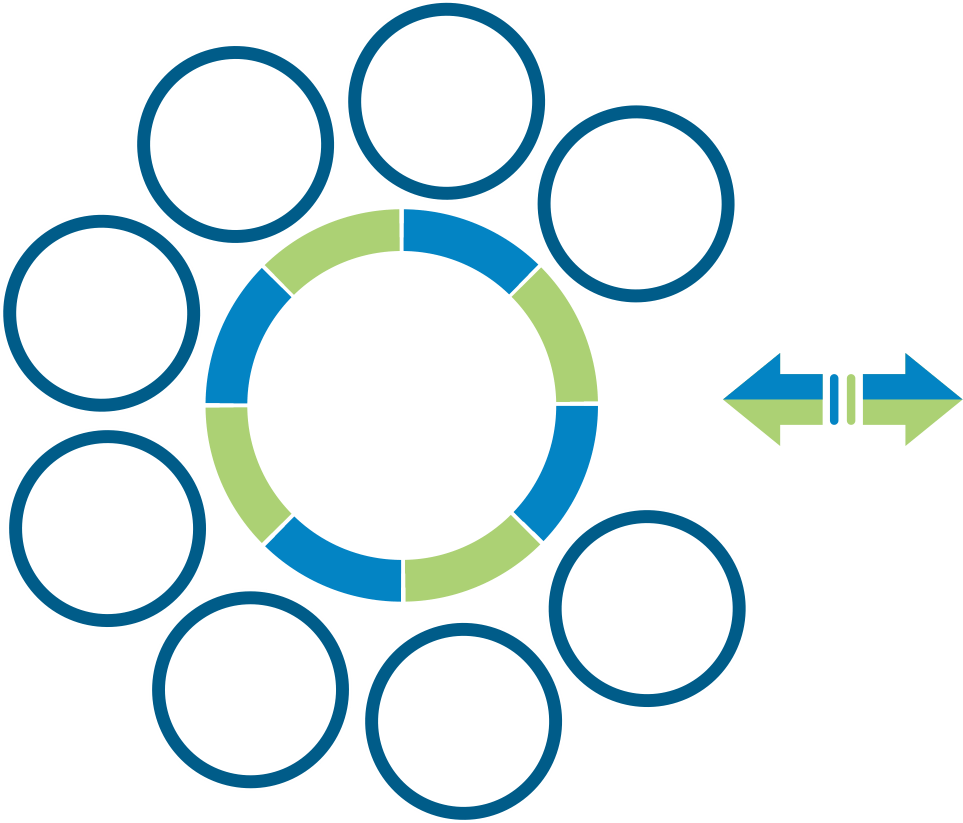

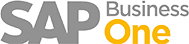
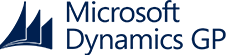
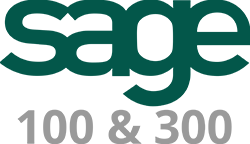
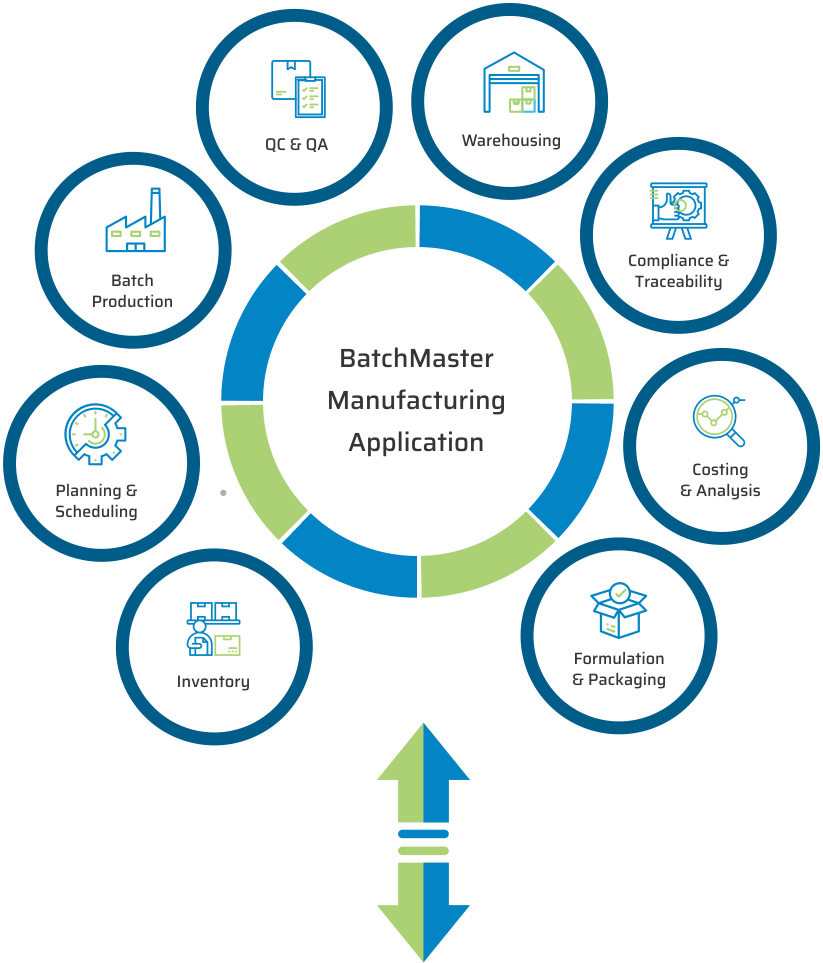

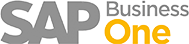
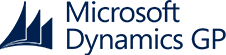

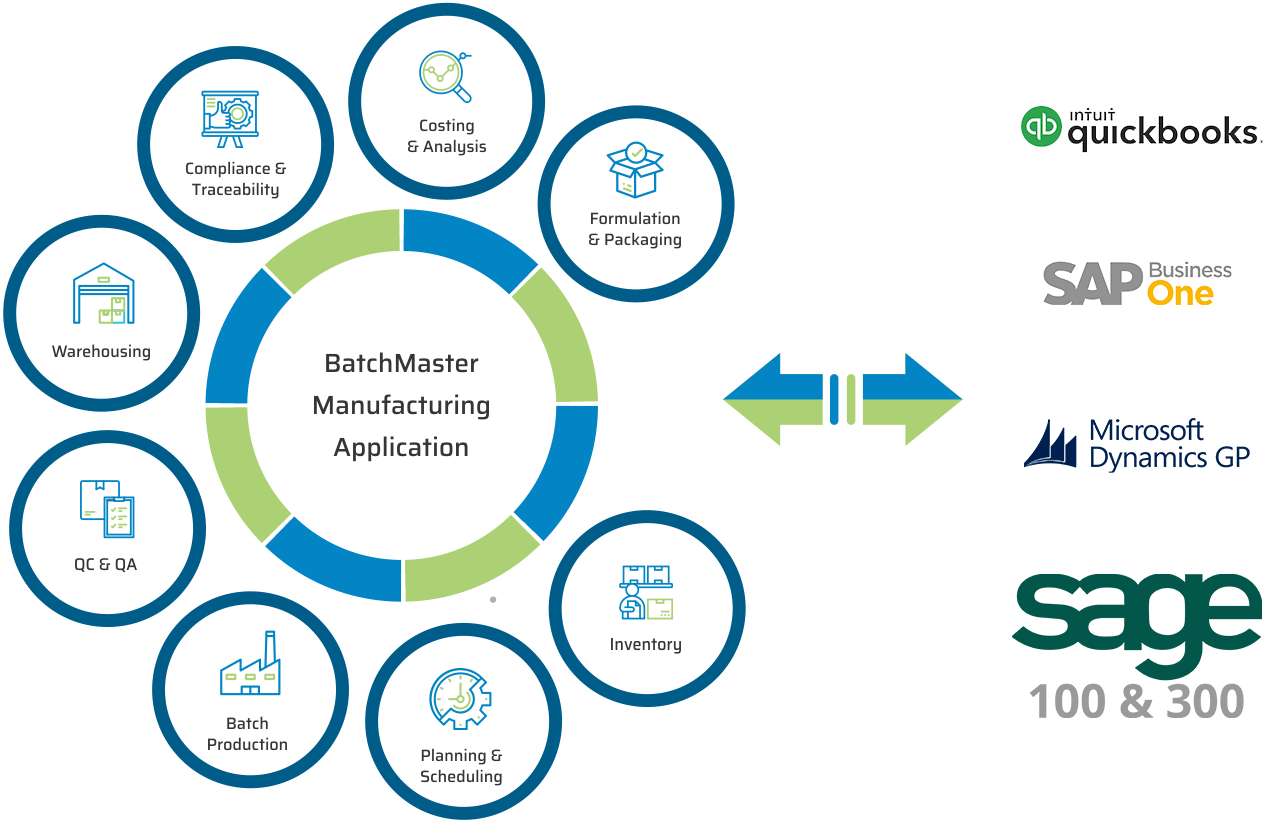
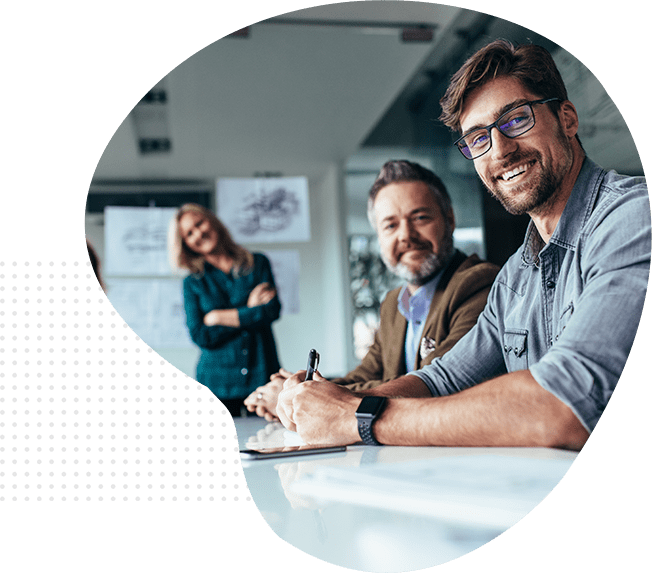
Upgrade to Batchmaster ERP for Your Industry

BatchMaster ERP is the enterprise resource planning system designed to meet all of your critical business needs within a single, cohesive platform.
BatchMaster ‘s best-in-class business and industry capabilities for manufacturing and distribution have been natively embedded into SAP Business One, SAP’s market-leading and future-proof platform for small and midsize enterprises
CONTACT US / REQUEST A DEMO

About Us

BatchMaster Software is a leading provider of Process Manufacturing ERP solutions that help companies worldwide meet their corporate objectives.
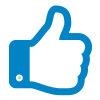
More than
2,000
Happy Customers
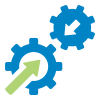
More than
2,500
Implementations
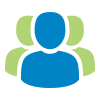
More than
40,000
Users
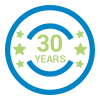
More than
30
Years of Experience
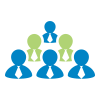
More than
500
Employees
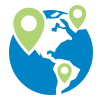
More than
7
Offices
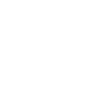
more than
40,000
Users
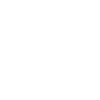
more than
30
Years of Experience