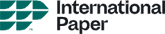
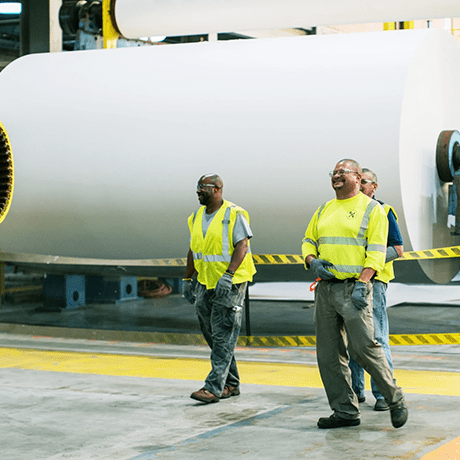
Company Name
International Paper
Location
Industry
Employees
BatchMaster Enables Global Supplier in Fulfilling Manufacturing Commitments, Saving Time and Money
International Paper (NYSE:IP) is a global paper and packaging company with manufacturing operations in North America, Europe, Latin America, Russia, Asia and North Africa. Its businesses include uncoated papers and industrial and consumer packaging, complemented by Xpedx, the North American distribution company. Headquartered in Memphis, Tenn., the company employs over 50,000 people in more than 20 countries. In 2008, International Paper purchased the CBPR (Containerboard, Packaging, and Recycling) Division of the global supplier of Weyerhaeuser, which grows and harvests trees, builds homes and makes forest products essential to everyday lives. At the time of the acquisition, Weyerhaeuser was a long-time user of BatchMaster Software’s solutions for everything from formula management to (today) Enterprise Resource Planning (ERP).
Within this very large organization is a water-based flexographic ink business with operations in 11 locations throughout North America, with nearly 100 employees who use BatchMaster Enterprise on any given day. The business objective of this ink division is to fulfill all the company’s customer requirements on-schedule and at agreed prices, at a profit. With major fluctuations in customer order patterns, these operations have maintain sizable safety stocks or had to be prepared to pay premium prices for delivery of short items if they were to meet customer requirements. As the scale of business grew, so did the severity of this problem.
Goals
- Leverage modern technology
- Integrate all departments
- Retire mainframe, eliminate spreadsheets
- Obtain a "Single Version of the Truth"
- Update inventory at batch close
Solutions
- BatchMaster ERP Coatings
Results
- Increased efficiency in formula management
- Reduction of errors in batch reporting
- Increased visibility and accuracy in inventory
In 1998, the staff realized that the manufacturing system, a semicustom mainframe-based inventory, sales, and purchase order management system, was no longer adequate to support their business. They then developed a list of criteria for their new system, which included immediate access to inventories from all ink manufacturing sites within the company (then 6).Further, they specified that inventories should be updated as batches were closed at the various plants by personnel on the floor rather than later by a separate administrative support group. This would reduce the time to update inventories and eliminate confusion and errors in entry. Of course, the product had to be easy to learn and use.
Time for a New System
Doug Miller, Lab Manager, first implemented the DOS version of BatchMaster years ago, in 1998. BatchMaster DOS met their criteria for real-time inventory control from multiple locations. Beyond that, Doug was excited about BatchMaster’s superior Lab and Formulation, offering Doug and his team substantial improvements in control and flexibility in formulations over the features of the legacy system and spreadsheets they’d been using to maintain thousands of formulations. Weyerhaeuser pressed ahead with increased reliance upon BatchMaster DOS until 2002 when they moved to BatchMaster Enterprise. Irene Jordan, the IT Manager supporting these operations, led a small team of inside consultants to work with BatchMaster’s consultants to accomplish this transition. Irene managed the modification or elimination of in-place procedural flows that had their roots in overcoming limitations of previous process automation software so that the company could take full advantage of BatchMaster Enterprise’s broad range of facilities.
These procedures were no longer required without the limitations imposed by an outdated manufacturing application. According to Irene, “The transition from DOS and Btrieve to Windows and MS SQL was certainly a challenge. But the BatchMaster support team worked diligently with us on all issues.”
Quick Quality Queries
One of the most important advances from the second to the fifth generation of BatchMaster is BatchMaster Enterprise’s foundation in Microsoft SQL. Doug routinely asks one of his in-house software analysts to develop a new “Crystal Report,” accessing SQL records in BatchMaster Enterprise, to better manage his business.
According to Doug, with BatchMaster, “you’re limited only by your imagination” regarding the inquiries you can make to support whatever analysis would be useful in managing your business. For example, Doug wanted to equip his Purchasing people with real-time access to inventory levels based upon closed batch orders, which are recorded individually throughout the work day. This was accomplished using a new Crystal Report, accessible at all times to all Purchasing personnel, regardless of location.
Real-time access to updated inventory allows Purchasing staff to avoid critical shortages and reduce the number of periodic adjustments in inventory for discrepancies between virtual and physical counts. Beyond these improvements, Purchasing staff can now consolidate orders for amore economical order quantity, manage inventory with greater confidence of not compromising production and service capability, and save money, too.
On the formulation side, SQL queries make possible the easy analysis of any “problem formula, ”that is, any formula with a plus or minus 10% content for critical ingredients so that Doug and his team can determine effectiveness and profitability with these formulas, and determine to continue or discontinue given products. Doug’s team makes heavy use, too, of “where used” and “physical properties” reports for global substitutions on the one hand and regulatory compliance on the other. Both reports result in substantial savings of time, and time is money in this case
“I'm sold on BatchMaster. It's a robust application, and it works.”
Today, BatchMaster provides all customers access to this data in dynamic Operational and Management Dashboards. Many of the reports that customers would once create can now be generated through the drag-and-drop display of data in dashboards. Areas such as inventory, shipping, receiving, sales, purchasing, and quality control have their dashboards showing either current or historical data, depending upon the users’ request. Once data displays are to the users’ satisfaction, unlimited numbers of user-configured reports can be stored and accessed on the fly, with the ability to export them to Microsoft Excel.
Procurement Pay-Off
Doug concluded, “I’m sold on BatchMaster Enterprise. It’s a robust application that works. BatchMaster Enterprise is the foundation for all the important decision-making for all our users to ensure quality, compliance, control costs and increase throughput.” Since their staff has continued to discover ways to streamline production and increase effectiveness with BatchMaster Enterprise, the company has added significant licenses to serve more users throughout North America. That and all the effort they’ve expended alongside their BatchMaster Software support team makes for an enduring commitment; committed to more throughput, better control, cost savings, and increased profitability. Appropriate to operations within a Fortune 500 company, should appeal to process manufacturing operations of any size, anywhere.