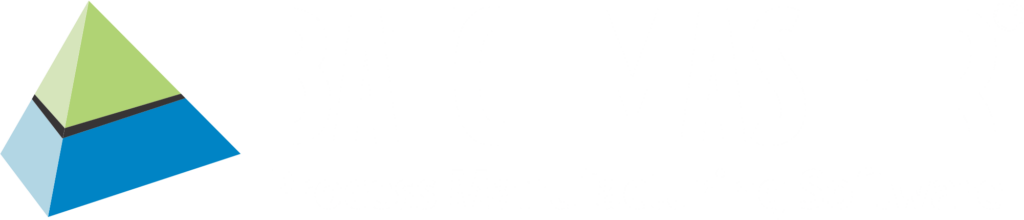
Food and Beverage Process Manufacturing ERP Software
Take a Product Tour

Best-in-class ERP for Food and Beverage Manufacturing Industry Verticals


Bakeries & Snack
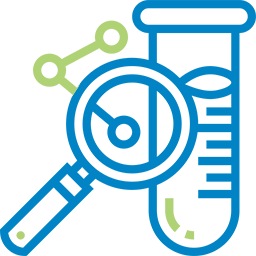
Chemical
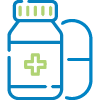
Life Science & Pharma

Bakeries & Snack

Beverages

Dairy

Dressings & Sauces

Spices &
Seasonings

Flavors &
Additives

Frozen &
Packed Foods

Confectionery &
Chocolate
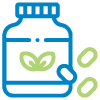
Nutraceutical
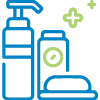
Personal Care & Cosmetic

Paint & Coating
Trusted by Leading Process Manufacturers Worldwide

Customer Success Spotlight: TEAAROMA

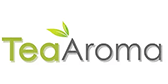
Logan Moon
You Need a Modern, Cloud-Based ERP to Scale Your Food and Beverage Manufacturing Operations

Process
Manufacturing
Modules
BatchMaster
ERP Solution
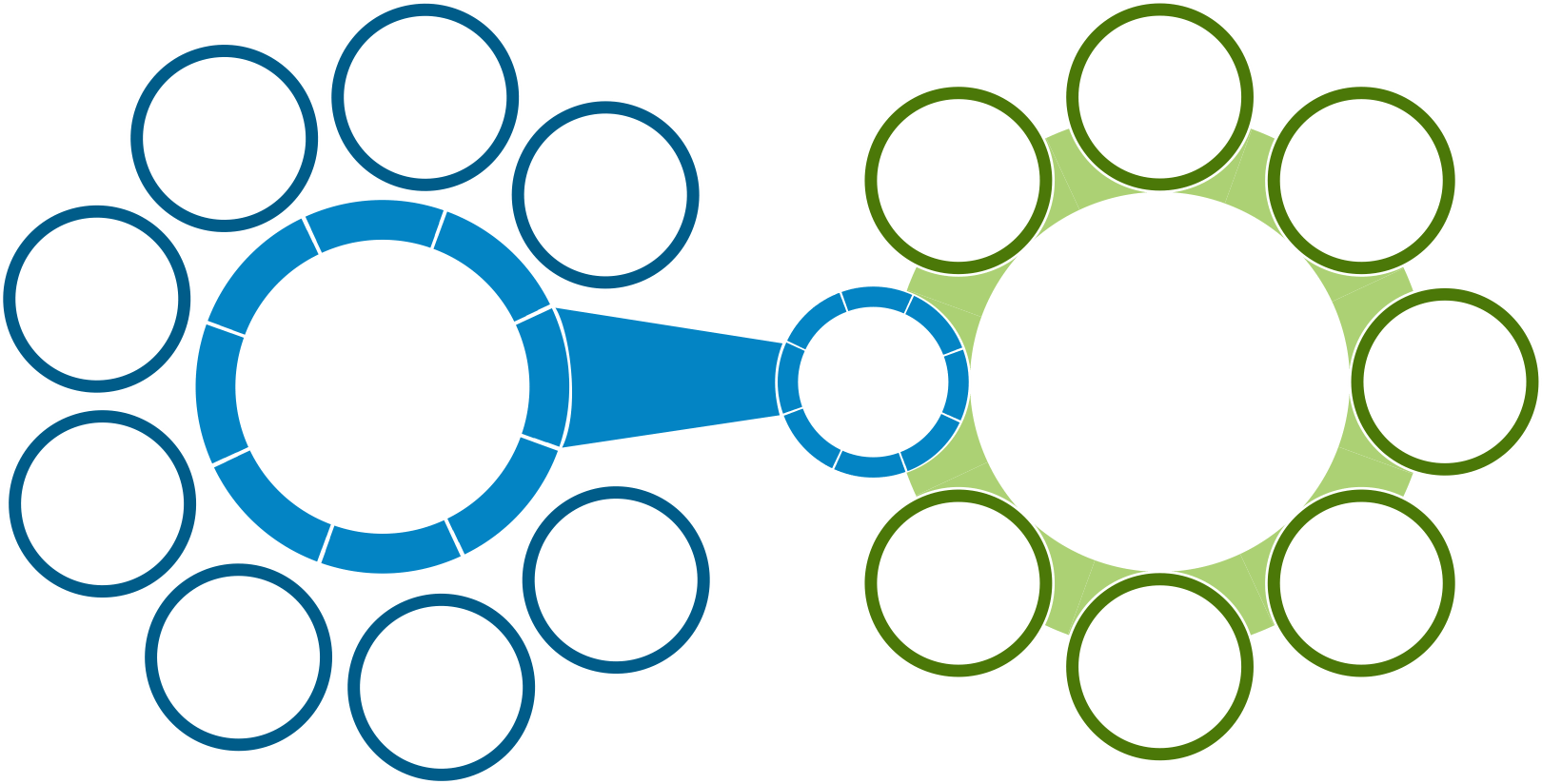
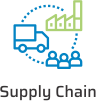
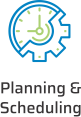

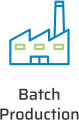


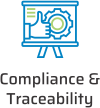
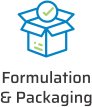
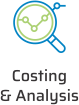
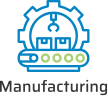


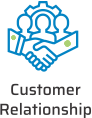


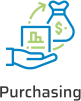
Why BatchMaster is the #1 Choice for Food and Beverage Manufacturers?

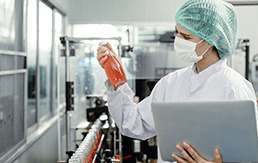
Industry Expertise

With over two decades of experience, BatchMaster understands the unique challenges of the food and beverage sector.
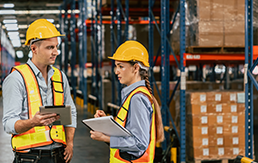
Tailored Solutions

Our web-based ERP system is highly customizable to meet the specific business needs of formula and recipe-based batch manufacturers.
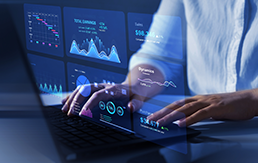
User-Friendly Interface

Modern, intuitive and easy-to-navigate dashboards and reporting tools make it simple for your team to leverage the power of our ERP system.
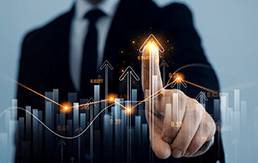
Scalability

BatchMaster scales with you as your business grows, accommodating increasing complexity and volume.
Industry-leading Capabilities Designed for Food and Beverage Manufacturers

- Inventory
- Traceability
- Quality Control
- Production
- Formulation
- Compliance
- Planning & Scheduling
- Mobile Warehousing
- Cost Analysis
Inventory
Efficient inventory management ensures seamless tracking and movement of ingredients, packaging, and finished goods, while monitoring quality control statuses, weights, and plant locations.
Key features include:
- Attribute Management: Maintain records for allergens, safety, certifications, and industry-specific documents.
- Smart Allocation: Allocate inventory based on expiry dates and quality status.
- Batch Adjustments: Dynamically adjust batch jobs according to inventory characteristics.
- Mobile Warehousing: Execute warehousing tasks efficiently using mobile devices.
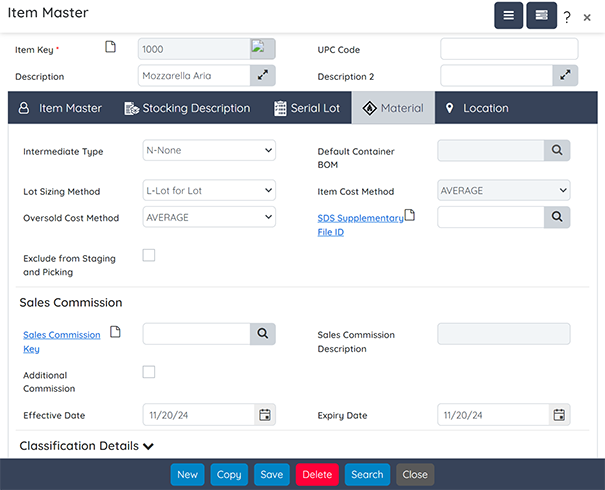
Traceability
Key features include:
- Automatic Lot Numbering: Assign lot numbers automatically during receiving and production.
- Lifecycle Tracking: Capture and validate lot numbers at every stage of production.
- Quick Searches: Perform bi-directional searches using an intuitive graphical tool.
- Recall Management: Generate barcoded labels (e.g., product labels, pallet licenses) to further streamline operations.
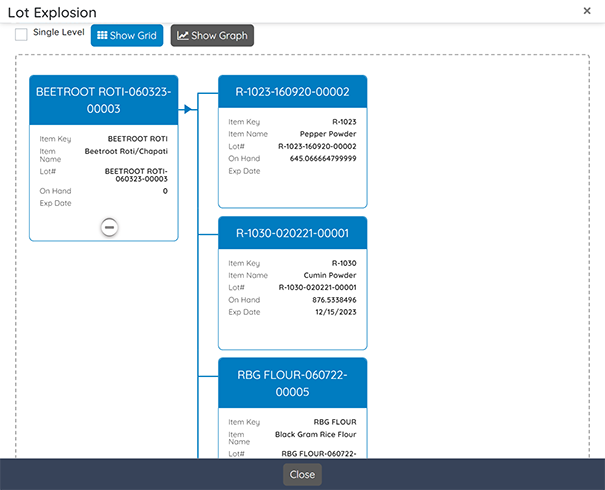
Quality
Integrate quality control and assurance throughout all processes, ensuring product safety and compliance.
Key features include:
- QC Testing: Set up quality control tests with specified tolerance and sample values.
- Inspection Plans: Execute comprehensive inspection plans and checklists.
- Documentation: Generate Certificates of Analysis (COA) and manage production deviations.
- Issue Management: Address customer complaints and nonconformance situations effectively.
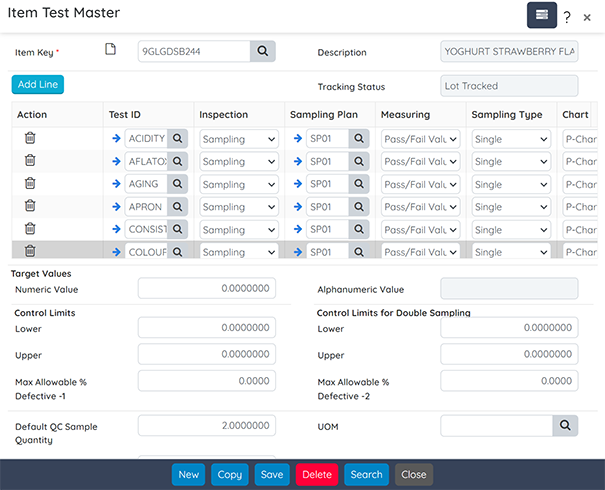
Production
Optimize production processes for intermediates and finished goods, including co-products and by-products.
Key capabilities include:
- Dynamic Job Scheduling: Link and schedule dependent batch jobs based on resource availability.
- Resource Management: Manage equipment capacities and resource allocations efficiently.
- Deviation Capture: Record and address deviations during production runs.
- Inventory Backflushing: Automatically backflush inventory for completed jobs.
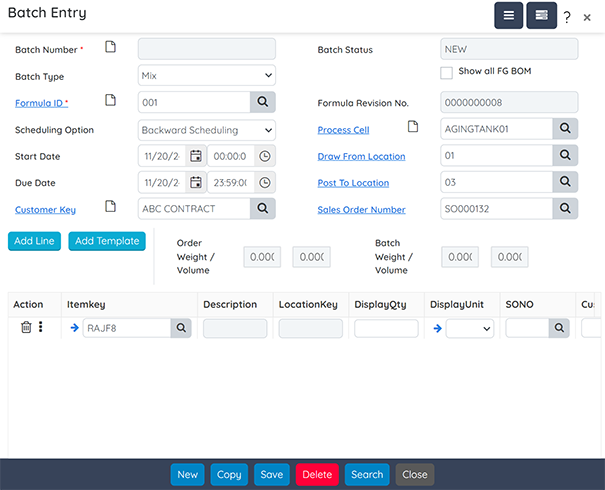
Formulation
Facilitate the management of product specifications across multiple versions and formulations.
Key features include:
- Dynamic Adjustments: Modify ingredient weights and volumes to achieve target properties.
- Cost Analysis: Account for fixed and variable labor and consumable costs.
- Specification Comparison: Analyze and compare different product specifications.
- Workflow Approval: Employ multi-level workflows for formulation approvals.
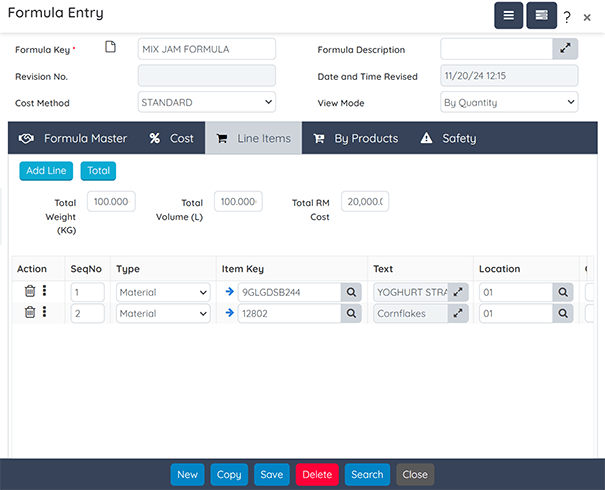
Compliance
Ensure adherence to federal and industry-specific regulations throughout every process.
Key functionalities include:
- Real-Time Alerts: Notify formulators when specifications exceed established levels.
- Data Capture: Mandate the collection of item, user, and location data for compliance (CFR 11).
- Audit Trail Maintenance: Maintain transactional history for auditor reporting, including Master Batch Records.
- Label Generation: Automatically generate required product and safety labels and documents.
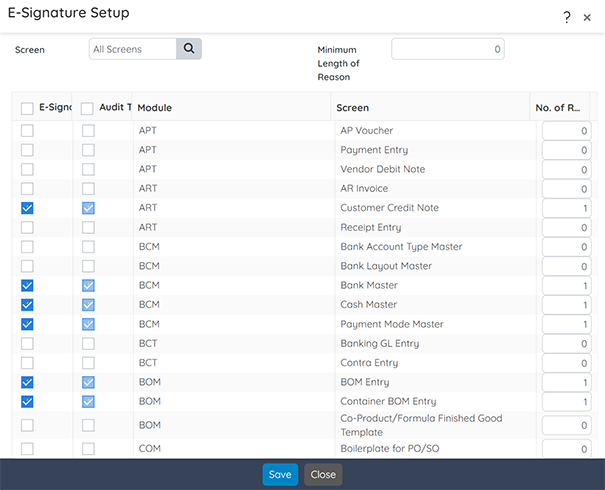
Planning & Scheduling
Optimize production and procurement processes to meet demand effectively.
Key capabilities include:
- Comprehensive Planning: Establish short, medium, and long-range planning periods.
- Facility Management: Plan production by facility or across multiple locations.
- Supply and Demand Consolidation: Streamline supply and demand management across facilities.
- What-If Analysis: Perform scenario analysis while planning production schedules.
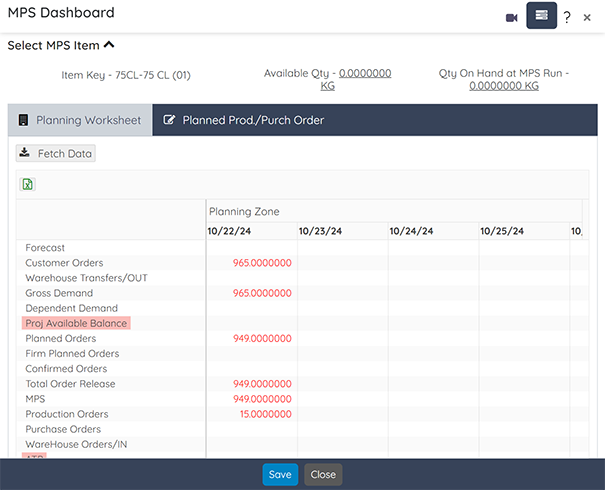
Mobile Warehousing
Key capabilities include:
- Batch Job QC Test: Capture QC information for inbound raw materials and WIP.
- Equipment Checklists and Inspections: Check the physical condition of on-hand inventory.
- Validate inventory location, license ID, lot number, and quantity.
- Generate required labels and reports: Generate barcoded labels (e.g. product labels and pallet licenses) to further streamline operations.
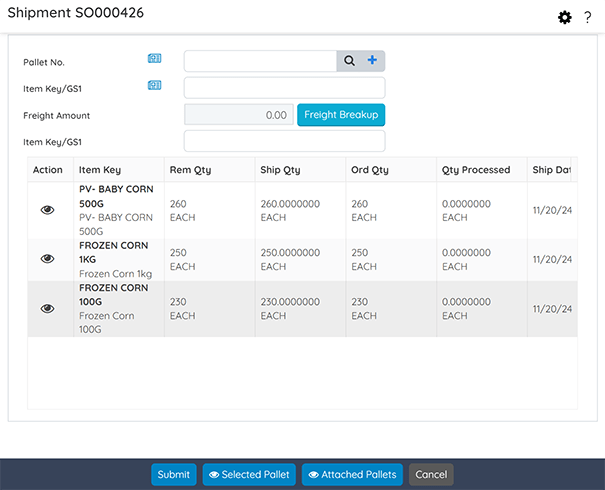
Cost Analysis
Balance consumer preferences with cost-effectiveness and production efficiency.
Key capabilities include:
- Comprehensive cost analysis of specifications
- Comparing costs associated with ingredients, labor, consumables, and additional shipping or miscellaneous expenses
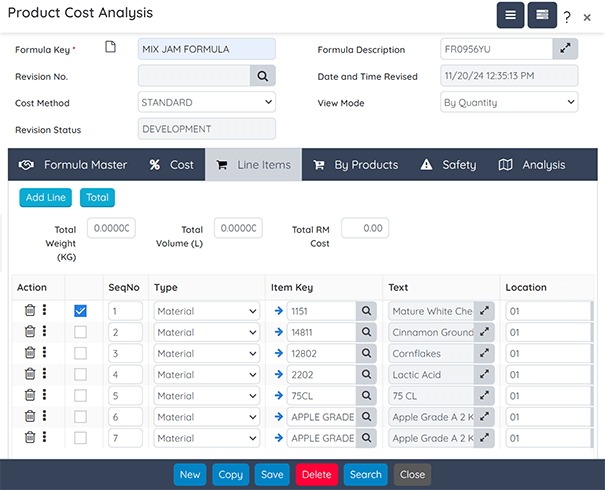
Inventory
Key features include:
- Automatic Lot Numbering: Assign lot numbers automatically during receiving and production.
- Lifecycle Tracking: Capture and validate lot numbers at every stage of production.
- Quick Searches: Perform bi-directional searches using an intuitive graphical tool.
- Recall Management: Generate barcoded labels (e.g., product labels, pallet licenses) to further streamline operations.
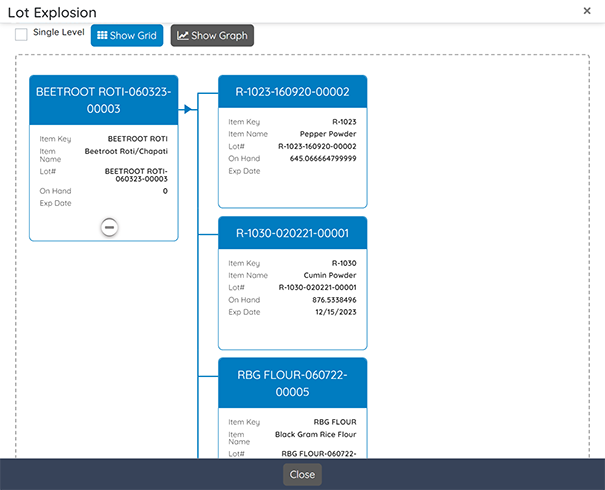
Quality
Key features include:
- QC Testing: Set up quality control tests with specified tolerance and sample values.
- Inspection Plans: Execute comprehensive inspection plans and checklists.
- Documentation: Generate Certificates of Analysis (COA) and manage production deviations.
- Issue Management: Address customer complaints and nonconformance situations effectively.
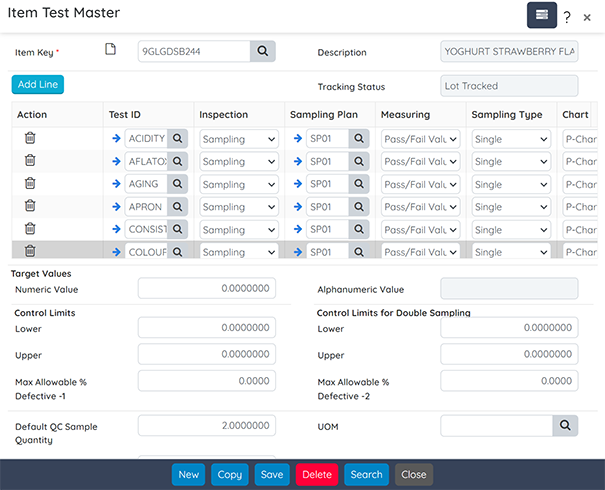
Production
Key capabilities include:
- Dynamic Job Scheduling: Link and schedule dependent batch jobs based on resource availability.
- Resource Management: Manage equipment capacities and resource allocations efficiently.
- Deviation Capture: Record and address deviations during production runs.
- Inventory Backflushing: Automatically backflush inventory for completed jobs.
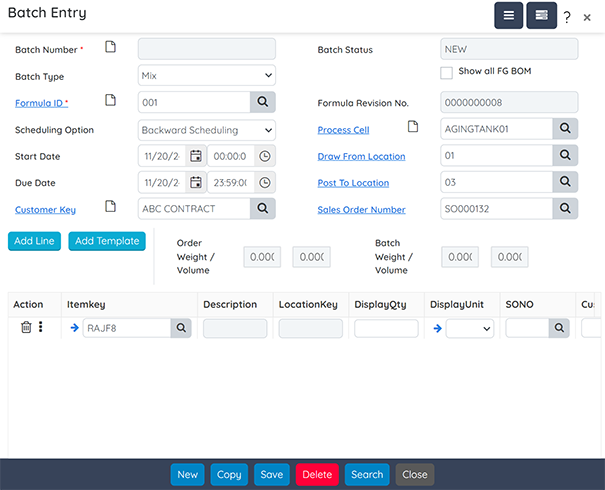
Formulation
Key features include:
- Dynamic Adjustments: Modify ingredient weights and volumes to achieve target properties.
- Cost Analysis: Account for fixed and variable labor and consumable costs.
- Specification Comparison: Analyze and compare different product specifications.
- Workflow Approval: Employ multi-level workflows for formulation approvals.
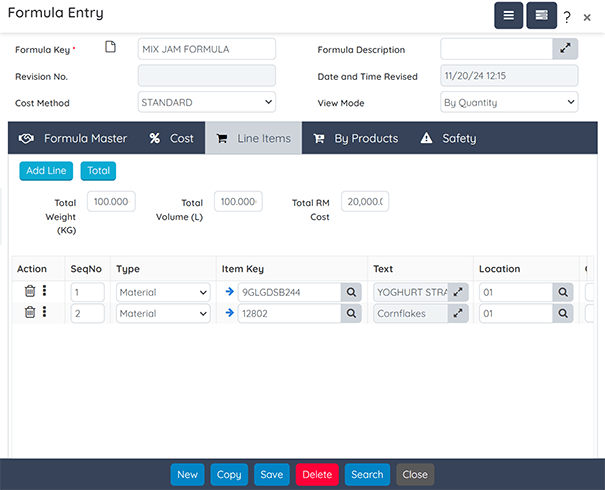
Compliance
Key functionalities include:
- Real-Time Alerts: Notify formulators when specifications exceed established levels.
- Data Capture: Mandate the collection of item, user, and location data for compliance (CFR 11).
- Audit Trail Maintenance: Maintain transactional history for auditor reporting, including Master Batch Records.
- Label Generation: Automatically generate required product and safety labels and documents.
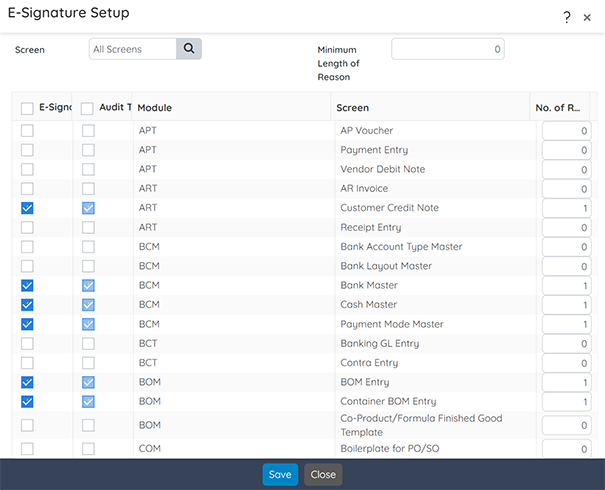
Planning & Scheduling
Optimize production and procurement processes to meet demand effectively.
Key capabilities include:
- Comprehensive Planning: Establish short, medium, and long-range planning periods.
- Facility Management: Plan production by facility or across multiple locations.
- Supply and Demand Consolidation: Streamline supply and demand management across facilities.
- What-If Analysis: Perform scenario analysis while planning production schedules.
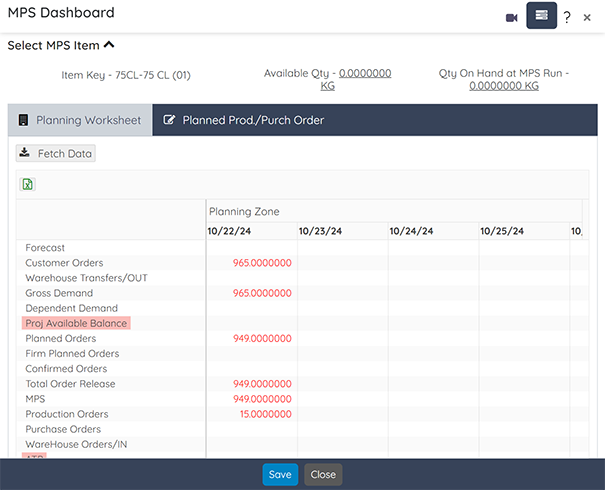
Mobile Warehousing
Key capabilities include:
- Batch Job QC Test: Capture QC information for inbound raw materials and WIP.
- Equipment Checklists and Inspections: Check the physical condition of on-hand inventory.
- Validate inventory location, license ID, lot number, and quantity.
- Generate required labels and reports: Generate barcoded labels (e.g. product labels and pallet licenses) to further streamline operations.
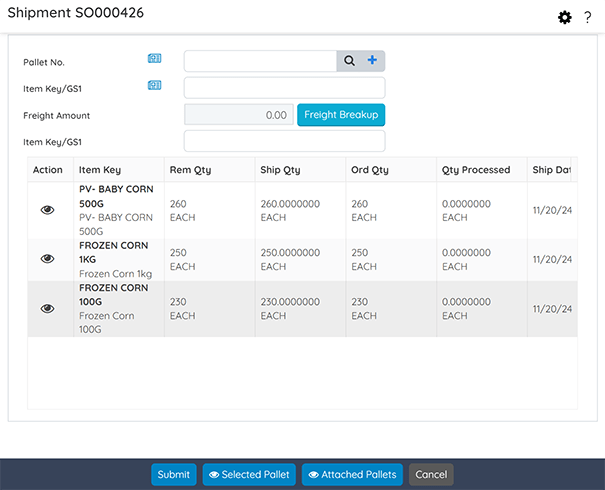
Cost Analysis
Key capabilities include:
- Comprehensive cost analysis of specifications
- Comparing costs associated with ingredients, labor, consumables, and additional shipping or miscellaneous expenses
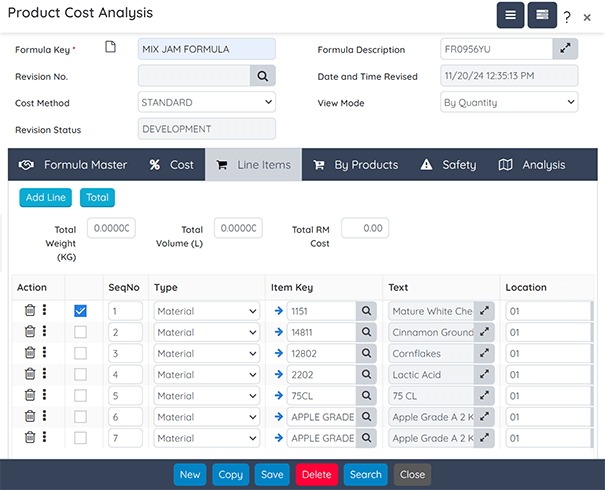
See What Food and Beverage Manufacturers Are Saying About BatchMaster

Diversified Foods and Seasonings, LLC
We evaluated nearly 15 ERP systems during our review period and selected BatchMaster Manufacturing because it could fill every need we had.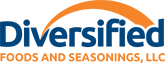
Cain Food Industries, Inc.
Cain Food Industries Inc. obtains improved lot traceability and function-rich formula module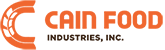
Michou Deli
It's super simple to use the platform. Customer on boarding was simple and payback time for this platform is short. I couldn’t be any happier. Look no further than BatchMaster – their team is knowledgeable and professional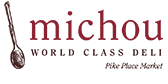
Metarom
We had a great experience with the BatchMaster implementation, and the support team. Everyone was very knowledgeable, and committed to helping us implement the system as fast as possible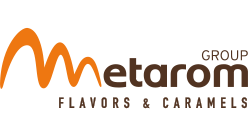
Newly Weds Foods International
With success in China, we decided to implement BatchMaster in Australia, with business two and half times that in China. Again, being successful in Australia also, we implemented in Bangkok and the Philippines as well. BatchMaster seems to be doing the job very well for us!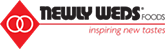
Diversified Foods and Seasonings, LLC
We evaluated nearly 15 ERP systems during our review period and selected BatchMaster Manufacturing because it could fill every need we had.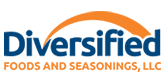
Cain Food Industries, Inc.
Cain Food Industries Inc. obtains improved lot traceability and function-rich formula module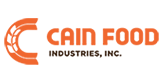
Michou Deli
It's super simple to use the platform. Customer on boarding was simple and payback time for this platform is short. I couldn’t be any happier. Look no further than BatchMaster – their team is knowledgeable and professional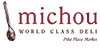
Metarom
We had a great experience with the BatchMaster implementation, and the support team. Everyone was very knowledgeable, and committed to helping us implement the system as fast as possible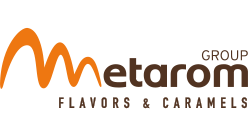
Newly Weds Foods International
With success in China, we decided to implement BatchMaster in Australia, with business two and half times that in China. Again, being successful in Australia also, we implemented in Bangkok and the Philippines as well. BatchMaster seems to be doing the job very well for us!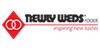
You Can Even Run BatchMaster with Leading Financial Applications

BatchMaster
Manufacturing
Application
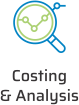
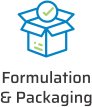
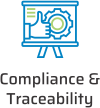


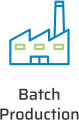
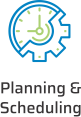

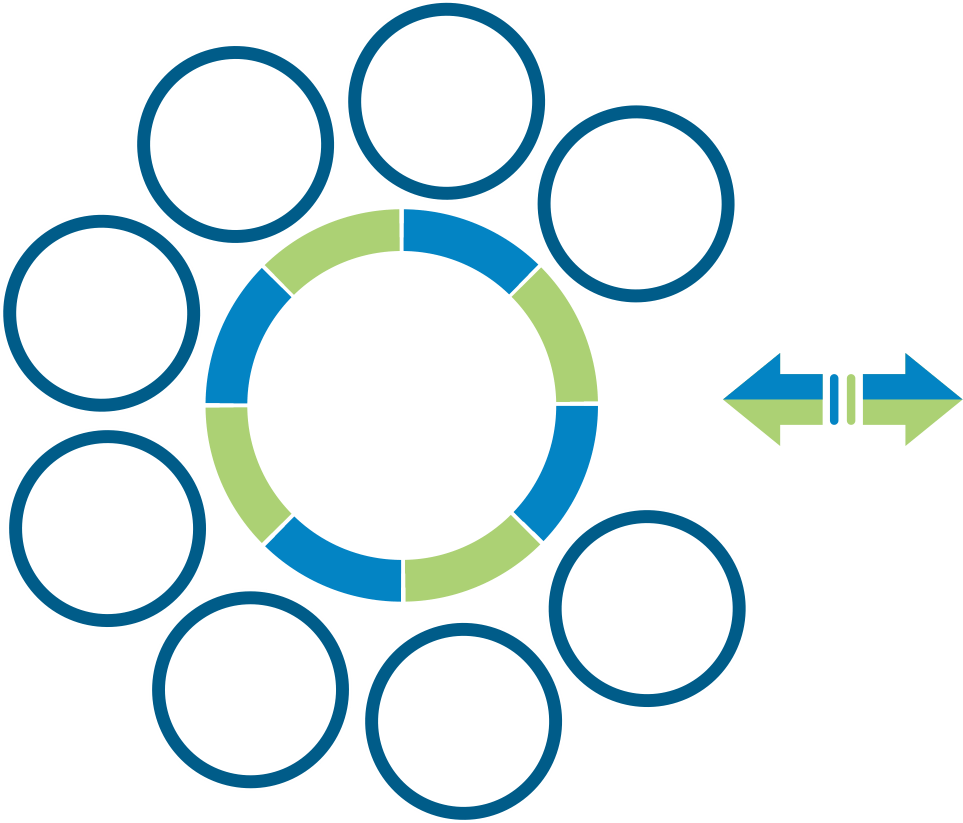

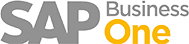
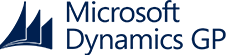
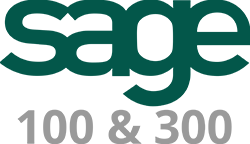
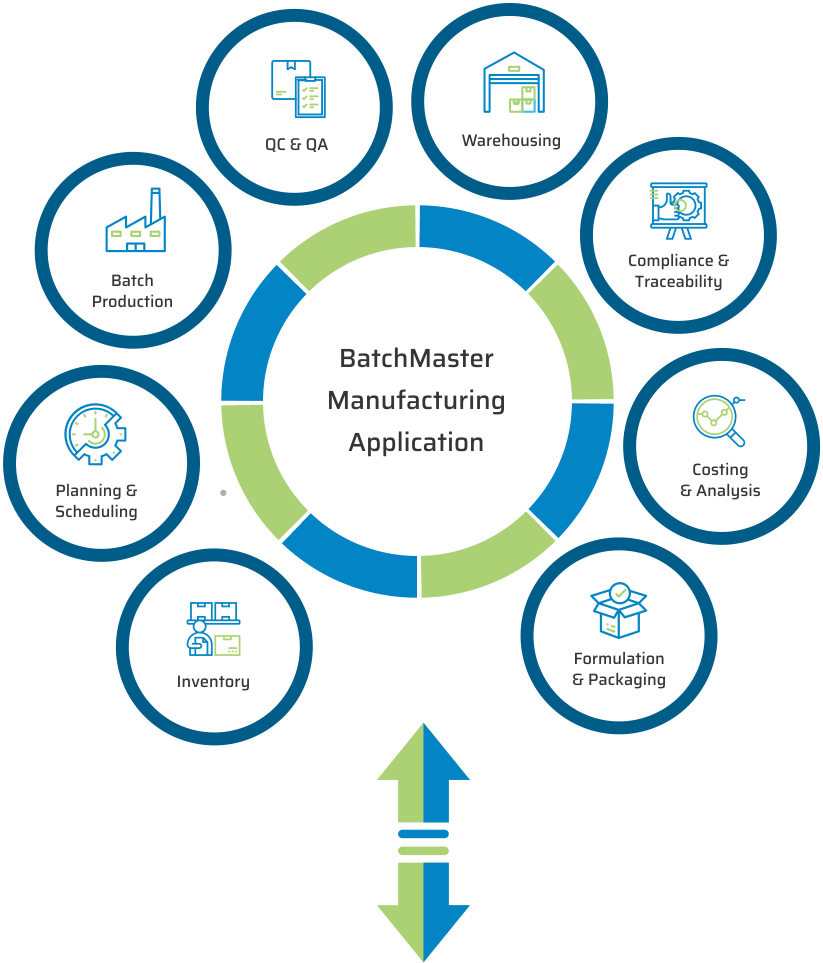

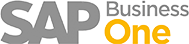
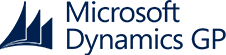

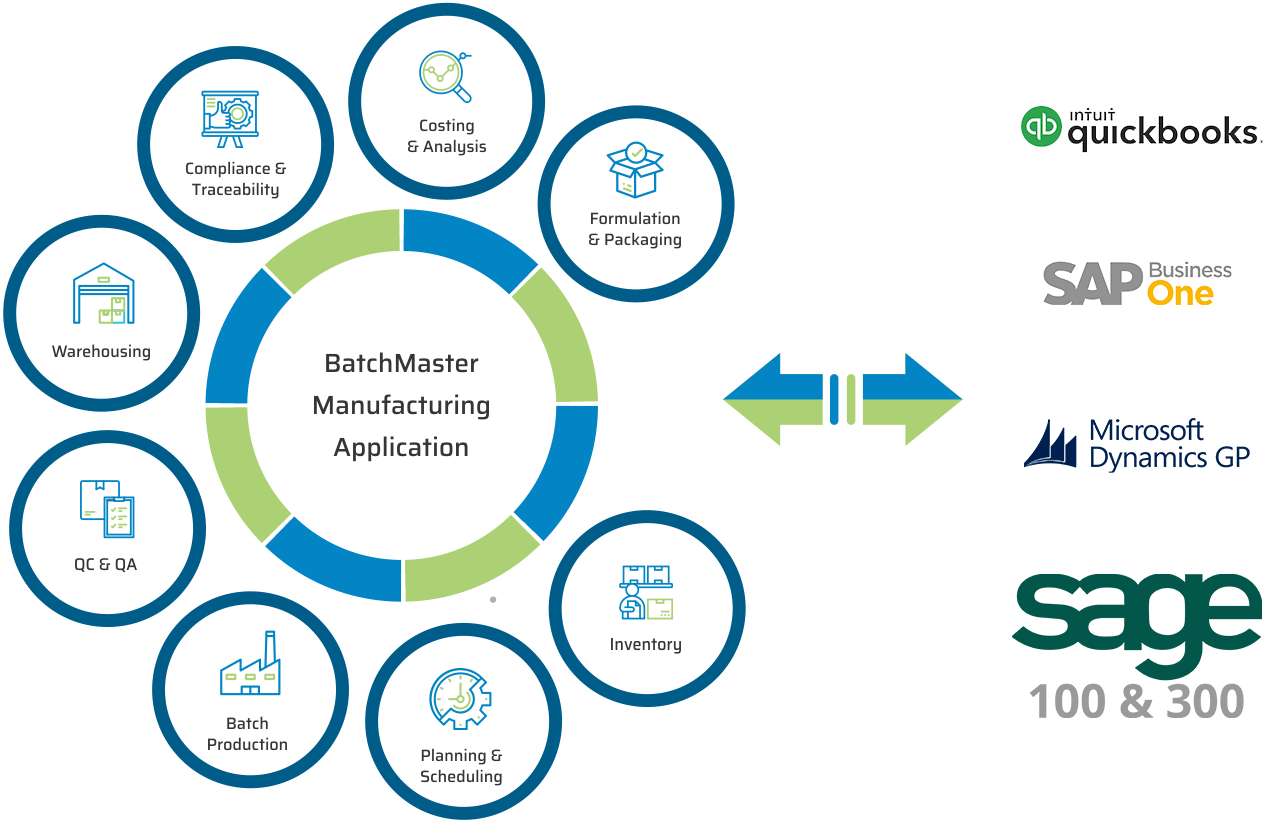
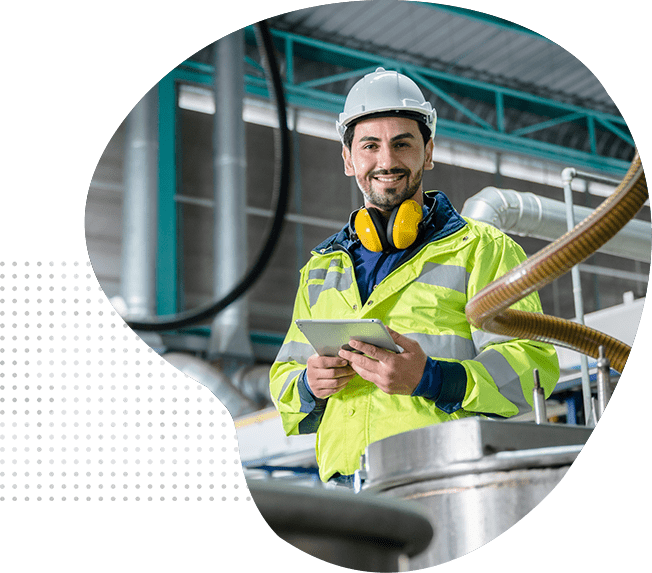
Upgrade to BatchMaster for Your Industry-Specific Manufacturing Requirements

Frequently Asked Questions

What challenges does BatchMaster help Food and Beverage manufacturers solve?
- Health Concerns: Adjust ingredient levels to meet nutritional targets and comply with health-conscious standards.
- Formulation Costs: Compare ingredient, labor, and shipping costs for informed decision-making.
- Fluctuating Prices: Get accurate cost estimates that account for commodity price fluctuations.
- Shelf Life Management: Optimize inventory use with expiration date tracking and rotation methods.
- Product Consistency: Manage ingredient variations to maintain quality and consistency.
- Supply Chain Disruptions: Adjust batch jobs based on raw material availability.
- Seasonal Demand: Automate batch job and purchase order forecasting based on seasonal demand.
- Regulatory Compliance: Ensure compliance with food safety standards and labeling requirements through built-in tools.
What are the key features of BatchMaster ERP?
Can BatchMaster integrate with my existing systems?
How does BatchMaster ERP enhance operational efficiency?
What kind of support and training do you offer?
About BatchMaster

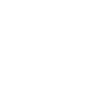
Specialized in Process Manufacturing ERP
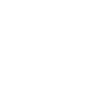
Industry leader for over 3 decades
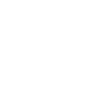
3,000+ customers
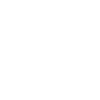
Services Offered – Process consulting, Integration, Support, Training, GMP/FDA validation
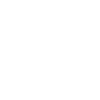